Saniline Case Study in a Leading Domestic Beverage Factory
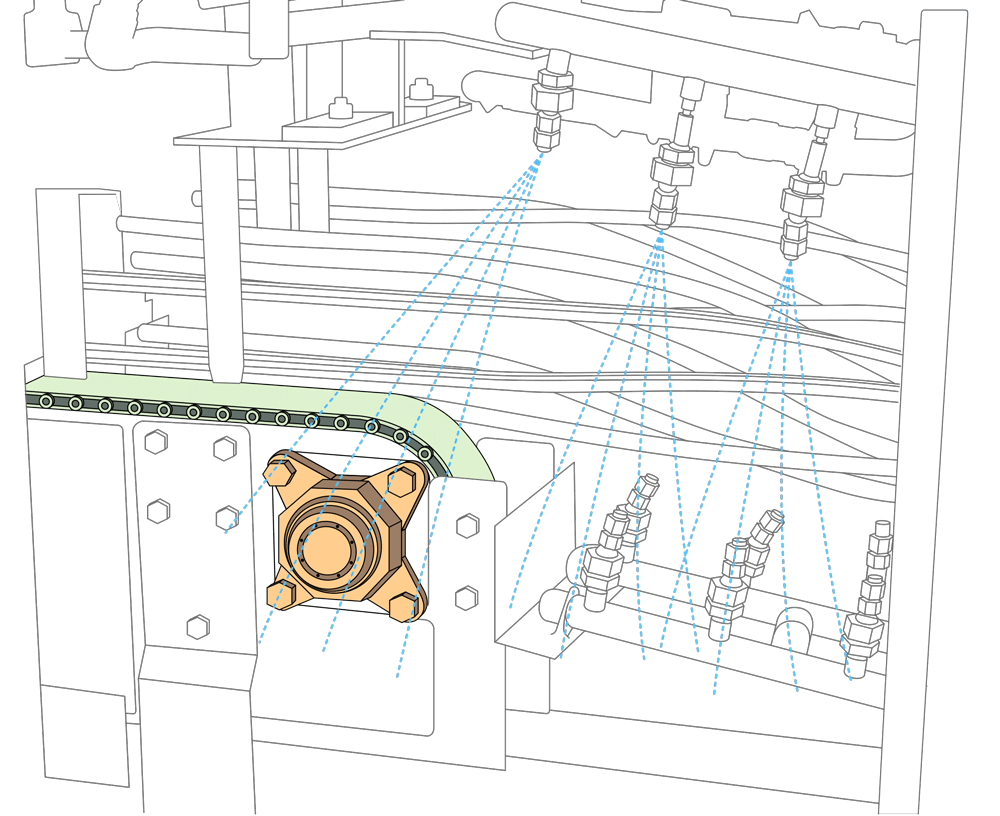
Although IP69K certification is typically conducted with bearings at rest, the following case demonstrates that waterproofing remains highly effective even during operation. The following report uses part of an internal report from a certain beverage factory dated June 2024.
April 2021: Due to conveyor replacement work associated with the installation of a foreign object inspection machine, the bearings in the affected area were changed to stainless steel bearing units from Company A, considering the impact of water spray, etc.
Company A’s stainless steel square flange unit, inner diameter 40 mm, with cover and NBR rubber plate between the unit and conveyor frame.
July 2021: The conveyor drive shaft stopped due to bearing failure. The failure was thought to be caused by a large amount of water entering the bearings. Although the use of corrosion-resistant stainless steel bearing units from Company A was anticipated, they failed in about four months. Downtime: approximately 200 minutes.
Restored with the same product from Company A.
Estimated Cause: Water from spraying and moisture from the conveyor scattered, and foam or hot water from equipment cleaning reached the bearings, causing moisture to penetrate inside. This likely led to grease degradation and oil film breakdown. The removed bearings were completely locked up.
Discussions with Company A did not yield effective countermeasures.
January 2022: Replaced with COC’s Saniline Series OCSF208.
The bearings from Company A removed at this time were dry, with a gritty feeling when turned by hand.
May 2024: After more than 18 months of use, no failures have occurred. Inspections using a stethoscope during idle operation showed no abnormalities.
Supplementary results from actual tests:
In October 2022, the seals were removed from a COC Saniline Series bearing after approximately 10 months of use for inspection.
The outer slinger was removed, and the grease sealed between the seals remained intact, with no water ingress.
The inner seal was also removed, and no water contamination was found, with a sufficient amount of grease still present inside the bearing.
Evaluation:
Compared to Company A’s stainless steel bearing units, which showed signs of failure or broke down after 4-5 months, the current bearings have lasted almost five times longer. The inspection results after about 10 months of use were also favorable.
With excellent waterproofing, these bearings have proven durable in harsh environments, making them highly effective as a preventive measure against recurrence. The superiority of COC’s bearings has been confirmed, and they are now being gradually applied to other conveyors as well.
Summary of Benefits:
1. Reduced downtime: Assuming continued use of Company A’s bearings, the risk of failure would persist around every four months. After switching to COC bearings, there have been no failures for over two years.
2. Reduced labor hours: Bearing replacement required 3 people x 3 hours. Performing this task three times a year (every 4 months) would have taken 27 hours, which has been saved.
3. Reduced unplanned repair costs: Fewer repairs also lower the risk of work-related injuries.